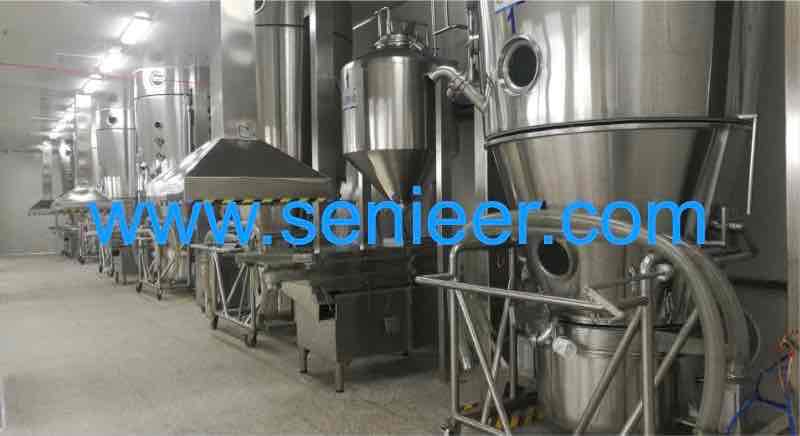
Are you wondering: “How does a Fluidized bed dryer (FBD) work?” and what is the application of fluidized bed dryer Today, I’ll take you through:
- Fluidized bed dryer parts
- Fluidized bed dryer diagram
- Fluidized bed dryer process
- Application of Fluidized bed Dryer
- Fluidized bed dryer advantages and disadvantages
- And more!
Why should you learn how a fluidized bed dryer (FBD) works?
Drying is a key unit process in chemical, food, and pharmaceutical industries. It requires heating making it capital and energy-intensive. In fact, drying may make up 60-70% of the total production cost.
Fluidized bed dryers have been widely adopted for drying granules and powders in solid dosage drug manufacture. Senieer produces very high-quality fluidized bed dryers at competitive factory prices.
Without further ado, let’s get started:
Chapter 1: What is a Fluidized bed dryer?
For better understanding, let’s examine each term in the phrase “Fluidized bed dryer.”Fluidize — It’s the process of making fine solid particles behave like particles of a fluid, which freely move about, slide past each other, and even collide with other molecules. Fluidization is done by suspending solid particles in a stream of fast-moving air.
Bed — Refers to the layer of suspended solid molecules.
Dryer — It’s the equipment where wet substances are dried.
To offer a quick summary:
In a fluid bed dryer, the inlet air stream is blown past solid powder molecules at rest. The particles are taken up in the dry & hot air stream and dehydrated through evaporation. Read on for the full explanation of the fluidized bed drying process.
Where are FBDs used? Application of fluidized bed dryer
You’ll find the fluidized bed dryer in pharmaceutical industries and application of fluidized bed dryer are humongous. Its main role includes drying granules produced by the wet granulation process. If you’re not familiar with this process, it simply involves agglomerating small powder particles together by using a granulating liquid solution.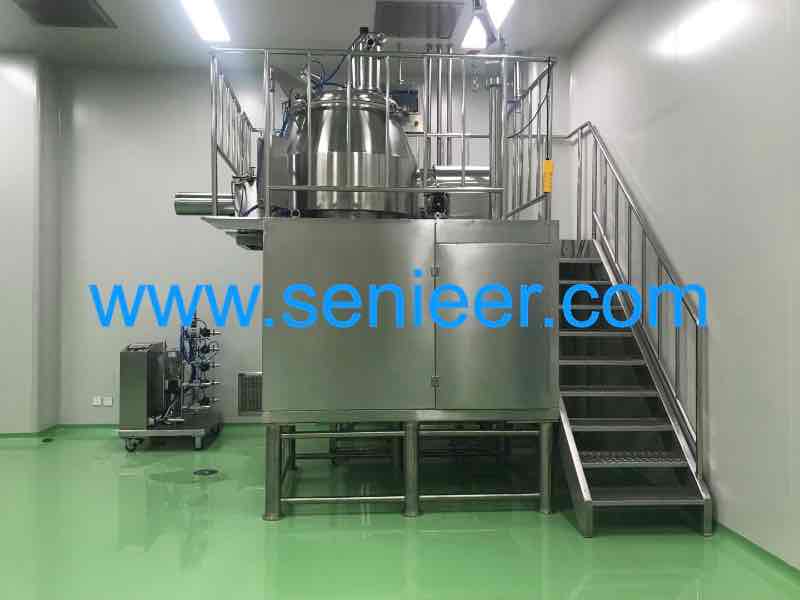
Part of the granulation solution includes a volatile solvent. We can eliminate this solvent by evaporating it in the dryer.
Other applications of the fluidized bed dryer equipment include:
- Food industries: Food processing, dehydration, and preservation such as drying chips
- Fertilizer industry: Drying of inorganic fertilizers such as calcium fertilizers.
Batch vs. Continuous-type fluid bed dryers (FBD):
Continuous fluidized drying means materials are flowing into the equipment, getting dried and discharged all without interrupting the process.And what do we mean by “batch drying?”
Batch drying implies that a fixed amount of material is fed into the dryer in one go. Drying is then carried out and when the endpoint is reached, the materials are discharged. You can also say that drying is done in sets or groups.
While continuous drying may have higher output rates, the pharmaceutical industry still relies on batch fluidized bed dryers (FBD).
Why are batch fluidized bed dryers still used?
Check out these four reasons:
1) Quality control & level of risk:
- For a continuous drying process, the process conditions must be strictly controlled. If not, a large quantity of material will get spoil. The continuous process also demands rigid monitoring. In batch processes, the material moves through the line in groups. If one batch gets damage, it’s just rejected without much loss.
- Better suited for heat-sensitive materials.
- More flexibility in that the sequence of unit operations can be switched or adjusted. It also offers better control over the process parameters.
- Continuous drying processes are still undergoing changes and development in the pharmaceutical industry. That’s why batch fluidized bed dryers will play a key role for a long time.
Other drying equipment you might encounter include:
- Static oven
- Rotary dryer
- Vacuum oven
- Microwave drier
- Spray drier
- Rotary atomizer
- I.R Drier
In this chapter, you learned about the basics of the fluidized bed dryer (FBD). Next, I’ll take you through the main parts of this drying equipment.
Chapter 2: Fluidized Bed Dryer Parts
For a good understanding of the fluid bed dyer’s working principle, you must know its parts. There are three systems, really:For instance, the main tower consists of the bowl, product container, bag filters, etc. You’ll learn about the function of each system along with its main components.
Let’s get started:
<a href="https://www.sigmatraffic.com?ref=66154">Buy cheap website traffic</a>
The AHU resembles a rectangular container. One end serves as the fresh air inlet. The other extends in a vent that links the AHU to the fluid bed dryer. Some components of the fluid bed dryer’s AHU include:
Primary filter (G4 filter)
The first filter medium is the G4 class filter. Its specification means it can remove airborne particles of 10μm.
You can see such particles with your naked eye. For instance, flower pollen. Senieer’s offers washable G4 filters that will save your costs.
Post-filter:
It’s the second filter mounted just after the primary filter. It deals with very fine dust and may remove particles as small as 1μm.
Dehumidifiers
There are usually two types of dehumidifiers:
First, the surface cooling dehumidification condenser coil. And second the wheel dehumidification unit. Now depending on the humidity of the air, they may be optional.
I’ll briefly explain how the wheel dehumidification unit works as the condenser coil is relatively easy to understand.
It’s also called the “Desiccant dehumidification wheel.” It consists of a wheel made up of corrugated material. The material on the wheel is a desiccant that attracts and retains water from the air.
You need the desiccant wheel when dealing with air with low humidity levels. Silica gel is an example of desiccant material used in the wheel.
Some AHU units have two dehumidifiers: The condenser coils are positioned before the wheel dehumidification unit.
Fan
It draws air from the surroundings inside the AHU unit past the filters and into the heating chamber.
Heating pipes
The next process after filtering and dehumidifying is heating. Cool incoming air absorbs heat from the surface of heated pipes. Now you may heat the pipes via steam or electricity. Our AHU comes with electric heating coils, but we also offer steam heating as an optional feature.
HEPA filter
Before the hot air leaves the UHA unit, it undergoes final filtering. For this, we use a high-efficiency HEPA filter. It can remove very small particles as small as 0.3 μm in diameter.
How is this possible?
The mechanical filter contains fibers arranged randomly forming a dense mat. And so you get an idea of what can be filtered: it removes tobacco smoke, bacteria, pigments, spores, etc.
The air stream coming into contact with the drug granules must be very clean and free from bacteria that’s why we need three filtering steps.
Other key components of the AHU include the sensors, differential pressure meter, control panel, etc.

Here are its main parts:
Base part (also called bowl/bottom chamber)
The base part connects to the AHU unit via a stainless steel tube ferrying the clean, hot & dry air. A butterfly valve along the air inlet tube stops the air intake when closed.
The base part also consists of the inlet air plenum. The plenum chamber facilitates the transfer of the air up the main tower.
Before production starts, the product chamber and the bottom chamber are interlocked. An inflatable gasket seal ensures the connection is airtight and leak-proof.
Next, let’s look at the product container.
Product container
As the name dictates, this container holds wet material that needs drying. It’s usually wet granules produced by the high shear mixer.
The product container comes with its own movable trolley. Sometimes it’s detached from the FBD and wheeled to the next process equipment such as the lifting column.
Another important feature of the product container is the bottom mesh/distributor plate. It’s held in place using SS clamps.
What is the distributor plate of FBD?
Just a mesh/metal screen with perforated holes. Its function is to resist airflow coming from the bottom chamber. Doing so, it evenly distributes air around the product container. The mesh also holds the product.
Other main features of the product container include:
- Viewing glass port (provides the operator with visual feedback)
- Sampling port (allows easy collection of samples from the product container)
- Product temperature sensor (Optional in some fluid bed dryers, but important for monitoring product temperatures)
Process chamber/retarding
It’s the area just above the product container. The connection between it and the product chamber is also made airtight with an inflatable gasket.
It’s the place in which fluidization takes place as air is drawn into the main tower past the bottom bowl and product chamber.
Expansion chamber and filter housing chamber
The expansion chamber forms the middle part of the tower. It’s integrated with the filter housing chamber that holds the double structure filter bag. Filter bags resemble sacks suspended over the process chamber.
Air flows upwards during fluidization and may carry in it small particles known as fines. The filter bags prevent fines from being exhausted.
The filtering bags become clogged with particles and require mechanical shaking to dislodge this dust layer. Shaking is done by pneumatic cylinders mounted at the top of the main tower.
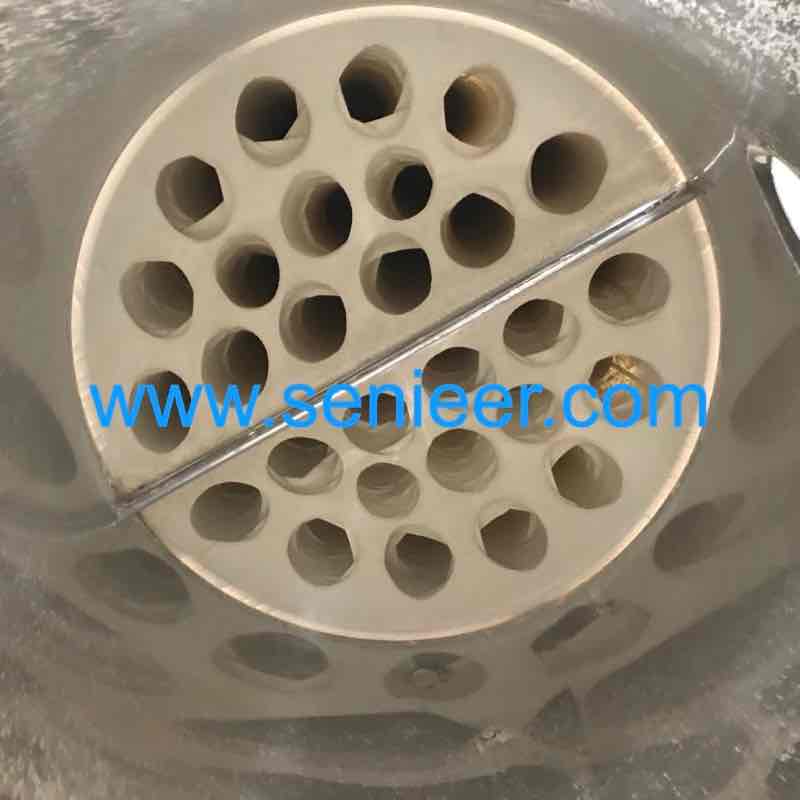
When used, it provides a higher filtering degree. Hence, more protection of the environment by reducing particulates in the exhaust gas. It’s also good when dealing with harmful substances needing the highest degree of containment.
During operation, the impeller rotates, which also causes the air molecules to rotate. The impeller also impacts centrifugal force on the air molecules causing them to move radially out.
On the outlet side, the air gains positive pressure and kinetic energy as it’s expelled. Inside the blower, displacement of air creates negative pressure. So more airflows into the blower. Centrifugal pumps are thus ideal for drawing air through resistance such as dampers, filter bags, etc.
Our blower comes with a dynamically balanced impeller. The blades are curved backward meaning they face away from the direction of the airflow. The FBD industrial blower also has an all-steel construction with anti-vibration mounting to make it quieter.
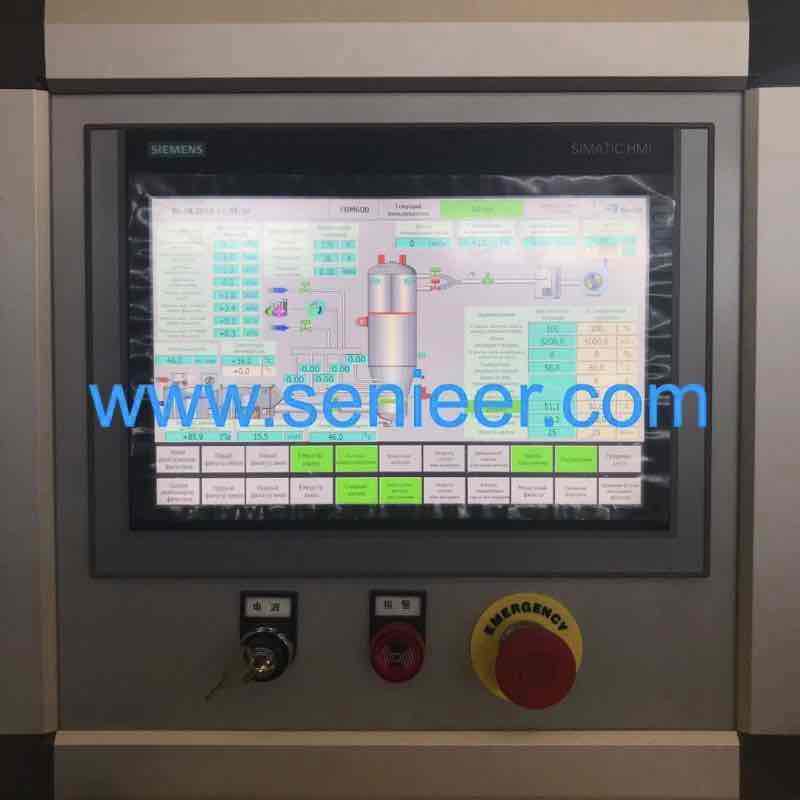
From the control panel, the operator can control the inlet temperature, set the filter bag shaking time, start & stop the blower motor, lift & lower the product chamber, read the exhaust temperature, and more.
Opting for a PLC automated control system makes controlling the drying process more efficient. Senieer’s fluid bed dryers also adopt Siemens intelligent touch input panel for better human-machine interfacing.
Earthing device: Prevents the danger of static electric electricity by absorbing and grounding the static charges.
In this chapter, you’ll discover exactly how the fluidized bed dryer works. We’ll also go over the factors influencing the drying rate.
What happens just before the drying process starts?
AHU preconditioning takes place along with warming up the main tower. Similarly, compression air inspections should be done to ensure that joints formed by inflation gaskets are leak proof.
Step 1: Loading
Loading of materials involves adding a fresh batch of wet granules into the product chamber. Through negative pressure feeding, materials can be sucked from the high shear mixer chamber through a feeding tube.
https://youtu.be/5nVSgadxLEA
Video showing vacuum conveying for fluid bed system
Step 2: Air inlet (intake)
Switching the blower unit on is done from the control panel. Once the blower is operational, the air is drawn continuously from the AHU unit and into the tower through the lower plenum.
Step 3: Fluidization
Inlet air is blown up through the static powder bed. As the velocity of the air increases so does the space between powder particles until the particles become suspended in a bed. The fluidization process is thought to occur in five stages including smooth fluidization, bubbling fluidization, turbulent fluidization, and fast fluidization.
Step 4: Drying
The drying process takes place in 3 stages until the endpoint is reached. (At the end-point the solid particle’s moisture level is equal or less than 1%):
Stage 1: Preheating
Wet particles are suspended in the hot and dry air stream. Moisture on the particles’ surface evaporates as heat flows through the body (conventional heating). The rate of drying slowly increases as the particles absorb more heat.
The moisture lost during preheating is still small. But the temperature of the bed rises steadily.
https://youtu.be/uh3XpMlwqUc
Fluid bed drying of Ibuprofen
Stage 2: Constant rate
Why is it called the constant rate?
The rate of drying remains constant as a function of time. In studies, plotting the amount of moisture lost against time gives a linear graph. In the preheating stage, the bed’s temperature was rising. But in this stage, the particles remain at the same temperature.
It’s case because any energy supplied is taken up by the evaporating molecules as they transition from the liquid to the gaseous state.
Most of the moisture is lost in this stage.
Stage 3: Falling rate stage:
Particles have lost most of their moisture and are nearing the drying end-point. With the surface moisture reduced, any remaining moisture is drawn from the porous core through capillary action.
Reduction in evaporation also causes the temperature of the bed to rise. Drying is stopped when the moisture level falls to less than 1%.
Step 5: Filter bags shaking
The blower continuously draws and excels air from the FBD. The air stream may contain very small particles called fines.
If they make it past the filter bags, they will be expelled into the surroundings. The filter bags capture the fines in their pores. But this causes the formation of a dust layer that clogs the filter bags causing a pressure drop.
Mechanical shaking is the best way to remove the dust layer, and it’s done by the pneumatic cylinders at the set intervals.
And since we have two filtering chambers, the shaking is alternated between the two.
Step 6: Exhausting & Secondary filtering unit (Optional)
Air exhausted from the FBD may go through a second filtering stage. This might help remove any particles that made it past the filter bag system.
Step 7: Discharging of dried material
Discharging refers to the removal of dried materials from the FBD. It can be done manually by unlocking and wheeling the product container on its trolley to the next process equipment.
Alternatively, vacuum conveying can be carried out by connecting the product container with a tube and creating negative pressure for suction using a vacuum transfer system.
After drying, the next process is milling carried out in the cone mill.
In a study, where the researchers increased the operating temperature from 60 to 80oC, there was a small increase in the drying rate. Though this was offset by the reduction in the energy efficiency of the FBD. So it’s always better to use the optimum operating temperature even if the drying time may be slightly prolonged.
Still increasing the air velocity may promote more mass and heat transfer. It may also improve the energy-efficient ratio, and reduce the drying time leading to less energy consumption.
Larger batch quantities will also need more time in the FBD than smaller batch quantities.
In summary, the main factors that influence the drying rate are:
Fluid bed dryer for drying tea.
Porosity defines the quality of a particle being porous or having small holes. With high porosity, liquids such as water have an easy time going through the tablet matrix. Once the liquid penetrates, it dissolves and disintegrates the tablet.
Disintegration and bioavailability are thus influenced by porosity. In addition, porosity influences:
What’s different about Senieer is that you can get very competitive pricing. We also offer more support and better after-sales services.
Senieer fluid bed dryer models include:
- FBD 600 Fluid Bed Dryer (Product container 600L, Production capacity 90kg to 270kg)
- FBD 400 Fluid Bed Dryer (Product container 400L, Production capacity 60kg to 180kg)
- FBD 300 Fluid Bed Dryer (Product container 300L, Production capacity 45kg to 135kg)
- FBD Laboratory Fluid Bed Dryer (capacity of 10L)
Our Lab Fluid bed dryer with programmable parameters, touch screen control, etc. Senieer also have 500kg fluid bed dryer, even more bigger, we can custom design for you.
For the best and lowest price, just send us a quote here.
Senieer can also offer a through-wall structure, among other custom solutions.
WhatsApp:
Skype: +8613637787586
Email: sales@senieer.com
Phone: +86-13637787586
WeChat: nikki201222
Check out our pharmaceutical machine videos: Senieer YouTube
Read More:
2.1. Inlet Air Handling Unit (AHU)
Function: “Supplying fresh, filtered, and heated air required for fluidizing & drying solid particles.”The AHU resembles a rectangular container. One end serves as the fresh air inlet. The other extends in a vent that links the AHU to the fluid bed dryer. Some components of the fluid bed dryer’s AHU include:
Primary filter (G4 filter)
The first filter medium is the G4 class filter. Its specification means it can remove airborne particles of 10μm.
You can see such particles with your naked eye. For instance, flower pollen. Senieer’s offers washable G4 filters that will save your costs.
Post-filter:
It’s the second filter mounted just after the primary filter. It deals with very fine dust and may remove particles as small as 1μm.
Dehumidifiers
There are usually two types of dehumidifiers:
First, the surface cooling dehumidification condenser coil. And second the wheel dehumidification unit. Now depending on the humidity of the air, they may be optional.
I’ll briefly explain how the wheel dehumidification unit works as the condenser coil is relatively easy to understand.
It’s also called the “Desiccant dehumidification wheel.” It consists of a wheel made up of corrugated material. The material on the wheel is a desiccant that attracts and retains water from the air.
You need the desiccant wheel when dealing with air with low humidity levels. Silica gel is an example of desiccant material used in the wheel.
Some AHU units have two dehumidifiers: The condenser coils are positioned before the wheel dehumidification unit.
Fan
It draws air from the surroundings inside the AHU unit past the filters and into the heating chamber.
Heating pipes
The next process after filtering and dehumidifying is heating. Cool incoming air absorbs heat from the surface of heated pipes. Now you may heat the pipes via steam or electricity. Our AHU comes with electric heating coils, but we also offer steam heating as an optional feature.
HEPA filter
Before the hot air leaves the UHA unit, it undergoes final filtering. For this, we use a high-efficiency HEPA filter. It can remove very small particles as small as 0.3 μm in diameter.
How is this possible?
The mechanical filter contains fibers arranged randomly forming a dense mat. And so you get an idea of what can be filtered: it removes tobacco smoke, bacteria, pigments, spores, etc.
The air stream coming into contact with the drug granules must be very clean and free from bacteria that’s why we need three filtering steps.
Other key components of the AHU include the sensors, differential pressure meter, control panel, etc.
2.2. Stainless steel main tower

Fluidized bed dryer (FBD) diagram
Function: “Fluidization and drying.”Here are its main parts:
Base part (also called bowl/bottom chamber)
The base part connects to the AHU unit via a stainless steel tube ferrying the clean, hot & dry air. A butterfly valve along the air inlet tube stops the air intake when closed.
The base part also consists of the inlet air plenum. The plenum chamber facilitates the transfer of the air up the main tower.
Before production starts, the product chamber and the bottom chamber are interlocked. An inflatable gasket seal ensures the connection is airtight and leak-proof.
Next, let’s look at the product container.
Product container
As the name dictates, this container holds wet material that needs drying. It’s usually wet granules produced by the high shear mixer.
The product container comes with its own movable trolley. Sometimes it’s detached from the FBD and wheeled to the next process equipment such as the lifting column.
Another important feature of the product container is the bottom mesh/distributor plate. It’s held in place using SS clamps.
What is the distributor plate of FBD?
Just a mesh/metal screen with perforated holes. Its function is to resist airflow coming from the bottom chamber. Doing so, it evenly distributes air around the product container. The mesh also holds the product.
Other main features of the product container include:
- Viewing glass port (provides the operator with visual feedback)
- Sampling port (allows easy collection of samples from the product container)
- Product temperature sensor (Optional in some fluid bed dryers, but important for monitoring product temperatures)
Process chamber/retarding
It’s the area just above the product container. The connection between it and the product chamber is also made airtight with an inflatable gasket.
It’s the place in which fluidization takes place as air is drawn into the main tower past the bottom bowl and product chamber.
Expansion chamber and filter housing chamber
The expansion chamber forms the middle part of the tower. It’s integrated with the filter housing chamber that holds the double structure filter bag. Filter bags resemble sacks suspended over the process chamber.
Air flows upwards during fluidization and may carry in it small particles known as fines. The filter bags prevent fines from being exhausted.
The filtering bags become clogged with particles and require mechanical shaking to dislodge this dust layer. Shaking is done by pneumatic cylinders mounted at the top of the main tower.
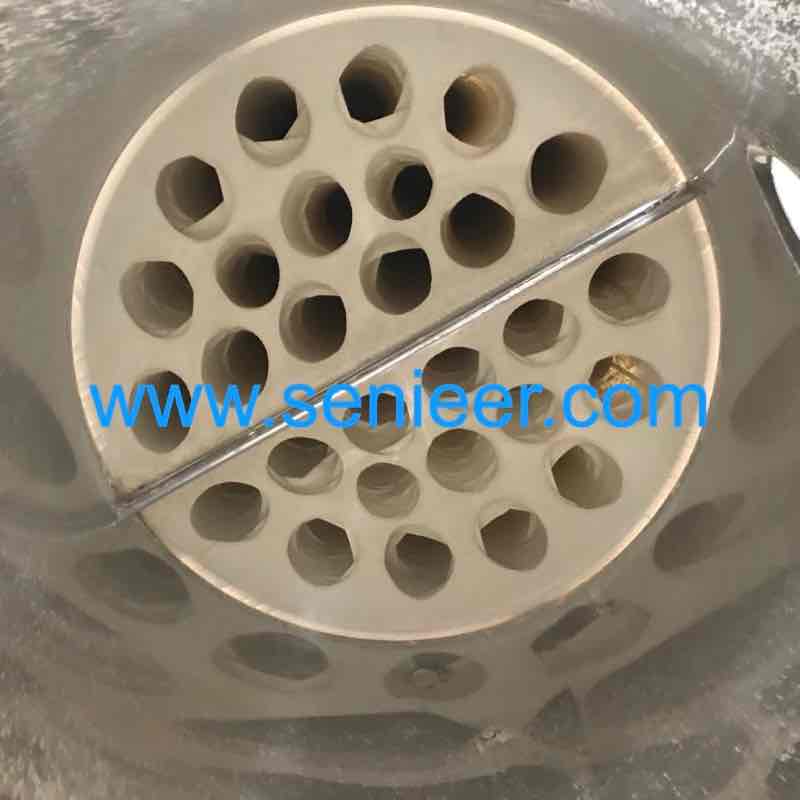
2.3. Exhaust piping connections
Two cylindrical pipes emerge from the expansion of the FBD from each side of the filter bags. They subsequently form into one vent that’s connected to the blower. They are fitted with dampers with actuators. The actuator is a device that moves the damper allowing the closure and opening of the vents; first, it must receive an electrical signal from the control system.2.4. Secondary filter unit/de-dusting unit (optional)
Some FBDs have a second filter unit. It captures fines that have passed through the filter bag system.When used, it provides a higher filtering degree. Hence, more protection of the environment by reducing particulates in the exhaust gas. It’s also good when dealing with harmful substances needing the highest degree of containment.
2.5. Draught fan/blower of FBD
In our fluid bed dryer, we use a centrifugal type blower. Its main parts include the impellers, drive shaft, drive mechanism (motor), casing and inlet & outlet ducts.During operation, the impeller rotates, which also causes the air molecules to rotate. The impeller also impacts centrifugal force on the air molecules causing them to move radially out.
On the outlet side, the air gains positive pressure and kinetic energy as it’s expelled. Inside the blower, displacement of air creates negative pressure. So more airflows into the blower. Centrifugal pumps are thus ideal for drawing air through resistance such as dampers, filter bags, etc.
Our blower comes with a dynamically balanced impeller. The blades are curved backward meaning they face away from the direction of the airflow. The FBD industrial blower also has an all-steel construction with anti-vibration mounting to make it quieter.
2.6. Control panel of FBD
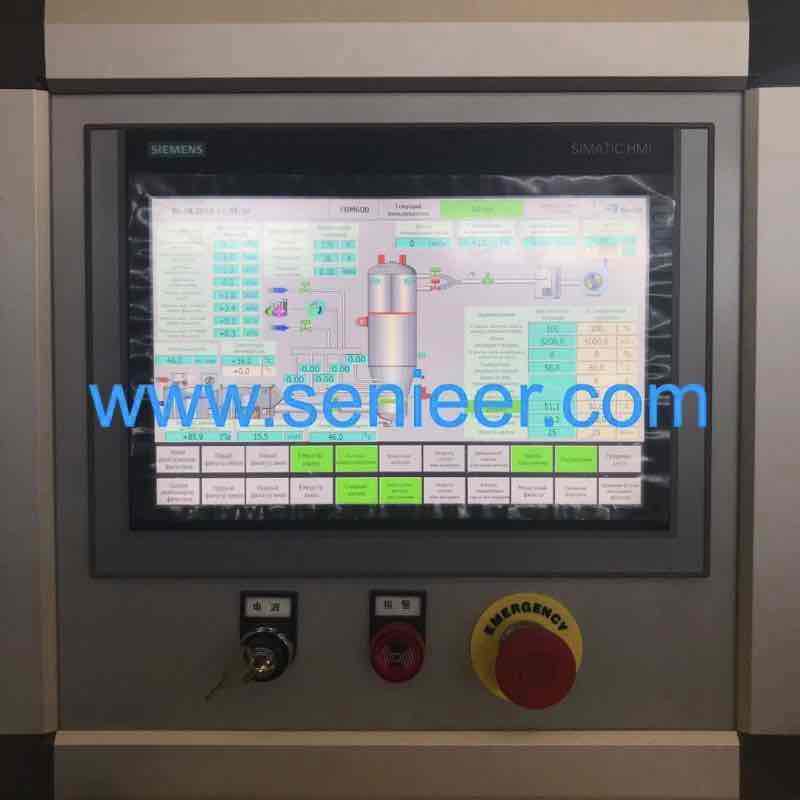
From the control panel, the operator can control the inlet temperature, set the filter bag shaking time, start & stop the blower motor, lift & lower the product chamber, read the exhaust temperature, and more.
Opting for a PLC automated control system makes controlling the drying process more efficient. Senieer’s fluid bed dryers also adopt Siemens intelligent touch input panel for better human-machine interfacing.
2.7. Other components
Other parts include the explosion vent/port that extends from the expansion chamber. It has a rapture disk tested at a pressure of 2 Bar(as optional item).Earthing device: Prevents the danger of static electric electricity by absorbing and grounding the static charges.
Chapter 3: Working principle of the fluidized bed dryer (FBD)
In this chapter, you’ll discover exactly how the fluidized bed dryer works. We’ll also go over the factors influencing the drying rate.
What happens just before the drying process starts?
AHU preconditioning takes place along with warming up the main tower. Similarly, compression air inspections should be done to ensure that joints formed by inflation gaskets are leak proof.
Step 1: Loading
Loading of materials involves adding a fresh batch of wet granules into the product chamber. Through negative pressure feeding, materials can be sucked from the high shear mixer chamber through a feeding tube.
https://youtu.be/5nVSgadxLEA
Video showing vacuum conveying for fluid bed system
Step 2: Air inlet (intake)
Switching the blower unit on is done from the control panel. Once the blower is operational, the air is drawn continuously from the AHU unit and into the tower through the lower plenum.
Step 3: Fluidization
Inlet air is blown up through the static powder bed. As the velocity of the air increases so does the space between powder particles until the particles become suspended in a bed. The fluidization process is thought to occur in five stages including smooth fluidization, bubbling fluidization, turbulent fluidization, and fast fluidization.
Step 4: Drying
The drying process takes place in 3 stages until the endpoint is reached. (At the end-point the solid particle’s moisture level is equal or less than 1%):
Stage 1: Preheating
Wet particles are suspended in the hot and dry air stream. Moisture on the particles’ surface evaporates as heat flows through the body (conventional heating). The rate of drying slowly increases as the particles absorb more heat.
The moisture lost during preheating is still small. But the temperature of the bed rises steadily.
https://youtu.be/uh3XpMlwqUc
Fluid bed drying of Ibuprofen
Stage 2: Constant rate
Why is it called the constant rate?
The rate of drying remains constant as a function of time. In studies, plotting the amount of moisture lost against time gives a linear graph. In the preheating stage, the bed’s temperature was rising. But in this stage, the particles remain at the same temperature.
It’s case because any energy supplied is taken up by the evaporating molecules as they transition from the liquid to the gaseous state.
Most of the moisture is lost in this stage.
Stage 3: Falling rate stage:
Particles have lost most of their moisture and are nearing the drying end-point. With the surface moisture reduced, any remaining moisture is drawn from the porous core through capillary action.
Reduction in evaporation also causes the temperature of the bed to rise. Drying is stopped when the moisture level falls to less than 1%.
Step 5: Filter bags shaking
The blower continuously draws and excels air from the FBD. The air stream may contain very small particles called fines.
If they make it past the filter bags, they will be expelled into the surroundings. The filter bags capture the fines in their pores. But this causes the formation of a dust layer that clogs the filter bags causing a pressure drop.
Mechanical shaking is the best way to remove the dust layer, and it’s done by the pneumatic cylinders at the set intervals.
And since we have two filtering chambers, the shaking is alternated between the two.
Step 6: Exhausting & Secondary filtering unit (Optional)
Air exhausted from the FBD may go through a second filtering stage. This might help remove any particles that made it past the filter bag system.
Step 7: Discharging of dried material
Discharging refers to the removal of dried materials from the FBD. It can be done manually by unlocking and wheeling the product container on its trolley to the next process equipment.
Alternatively, vacuum conveying can be carried out by connecting the product container with a tube and creating negative pressure for suction using a vacuum transfer system.
After drying, the next process is milling carried out in the cone mill.
Parameters that influence drying
The rate of drying depends on several factors including the product’s characteristics, process parameters, and even the design of fluid bed dryer (FBD). For instance:- Position of the air distribution plate — It has a direct bearing on the airflow pattern inside the fluid bed dryer.
- The body’s shape —The shape of the tower has also been shown to impact the drying rate with an annular shape preferred.
- Temperature of the inlet air
In a study, where the researchers increased the operating temperature from 60 to 80oC, there was a small increase in the drying rate. Though this was offset by the reduction in the energy efficiency of the FBD. So it’s always better to use the optimum operating temperature even if the drying time may be slightly prolonged.
- Humidity of the air
- Flow rate of air (Air Flux)
Still increasing the air velocity may promote more mass and heat transfer. It may also improve the energy-efficient ratio, and reduce the drying time leading to less energy consumption.
- Product parameters:
- The products moisture content
- Amount of product loaded
Larger batch quantities will also need more time in the FBD than smaller batch quantities.
In summary, the main factors that influence the drying rate are:
- The flow rate of inlet air
- The amount of material loaded into the FBD.
Chapter 4: Fluidized bed dryer (FBD) advantages and disadvantages
The fluidized bed dryer produces quality granules. These granules have high porosity, and in the pharmaceutical industry this is very important for a number of reasons:Porosity defines the quality of a particle being porous or having small holes. With high porosity, liquids such as water have an easy time going through the tablet matrix. Once the liquid penetrates, it dissolves and disintegrates the tablet.
Disintegration and bioavailability are thus influenced by porosity. In addition, porosity influences:
- Shelf life of the drug
- Compression performance during tableting
- Dissolution rate
- Pharmacokinetic behavior
- Fluidized bed dryer (FBD) achieves faster drying rates with the drying time ranging from 20 minutes to 40 minutes.
- With the material in a fluidized state, there are no hot spots.
- It enhances the product’s properties I.e. its porosity.
- FBD dryers don’t have lots of moving parts and require little maintenance.
- It offers high containment of material, and still offers viewing and sampling ports allowing the operator to monitor the process easily. Sensors also provide constant feedback on process parameters such as the product temperature, outlet air temperature and inlet air temp, allowing the PLC control to make any adjustments as required.
- It’s suited for thermosensitive products because you can operate it at relatively low temperatures. For instance, the air is usually at 60o The product doesn’t come into contact with hot surfaces minimizing the likelihood of the powder material getting burned.
- With PLC control and using touch screen inputs for programming the process parameters, the FBD is easy to use, less labor-intensive and gives consistent results.
- The drying is uniform. And by using the AHU, it’s easy to regulate the temperature of the air stream.
- Electrostatic charges tend to develop on the particles, which will impair fluidization. But Senieer FBD machines overcome this problem through sufficient earthing.
- Sometimes the materials might shrink on contact exposure to high temperatures, but with our capable control system, it is simple to maintain the perfect fluidizing conditions.
- The vessel gets subject to lots of pressure, which might increase the risk of accidents. Though, we offer explosion-proof designs of 10 bar or 12 bar.
- In the fluidized state, particles are constantly colliding with each other leading to attrition. Considerable particle size reduction will result in very fine powders. Senieer’s FBD equipment is adapted to solving this problem by minimizing the residence times. You can also reduce attrition by using suitable binding agents.
Chapter 5: Where to find a Fluidized bed dryer?
Senieer offers state of the art fluid bed drying units for a wide range of applications. You’ll find every feature in our models as in similar international brand items. On-going research and development ensure we improve the fluid bed drying machines.What’s different about Senieer is that you can get very competitive pricing. We also offer more support and better after-sales services.
5.1. Senieer Fluid Bed Dryer Models:
We have different sizes and models for your production needs. The company can also offer turnkey solutions (custom FBDs) since we have the factory and technical team to handle your order.Senieer fluid bed dryer models include:
- FBD 600 Fluid Bed Dryer (Product container 600L, Production capacity 90kg to 270kg)
- FBD 400 Fluid Bed Dryer (Product container 400L, Production capacity 60kg to 180kg)
- FBD 300 Fluid Bed Dryer (Product container 300L, Production capacity 45kg to 135kg)
- FBD Laboratory Fluid Bed Dryer (capacity of 10L)
Our Lab Fluid bed dryer with programmable parameters, touch screen control, etc. Senieer also have 500kg fluid bed dryer, even more bigger, we can custom design for you.
5.2. What is the Fluid bed dryer (FBD) price?
The cost of the equipment depends on the model’s production capacity along with the options you select. For instance, you can opt for the 10 Bar explosion-proof FBD design that’s more expensive than the 2 Bar FBD.For the best and lowest price, just send us a quote here.
Senieer can also offer a through-wall structure, among other custom solutions.
5.3. 10 more reasons to buy Senieer’s Fluidized bed dryer (FBD)
- Key selling point: Senieer’s fluid bed equipment offer stable, uniform and high performance.
- Get a wide range of models with maximum product capacities of 4.5kg-450kg, others can custom design for you.
- Custom-made Fluid bed dryers are available.
- cGMP compliant.
- Stable construction with stainless steel sheets. We use S.S 304 with a thickness of 3-4mm for the bottom chamber and other non-contact parts. Contact parts adopt SS 316L. We use the right thickness allowing the FBD to withstand high pressures and last longer.
- Modular design with single-piece construction.
- Capable of fluidizing materials of different densities.
- Easy to clean with WIP system available as an option: The FBD also has no dead corners.
- Air handling unit has a high automation level.
- Siemens touch screen control panel with programmable and printable parameters.
5.4. Why Senieer can offer you the best services for FBD
- We are a leading pharmaceutical supplier for over 30 years.
- Consistent sales and excellent after-sales service.
- Quick online support for all your inquiries in less than 12 hours.
- Engineers available for installation support and servicing the FBD machine overseas.
WhatsApp:
Skype: +8613637787586
Email: sales@senieer.com
Phone: +86-13637787586
WeChat: nikki201222
Check out our pharmaceutical machine videos: Senieer YouTube
Read More:
Acme Process Systems Pvt. Ltd., Pune, India is one of the leading Agitator Manufacturers in India, Top Agitator Manufacturers In Pune.
ReplyDeleteThey are also best Reactor Manufacturers India, Heat Exchanger Manufacturers India.
They cater top pharmaceutical, Chemical, Paint companies around the world.
Get more information form website www.acmeprocess.net
Thanks for sharing this information with us. It is really helpful for us. Keep sharing this kind of informational and knowledgeable blog. We Titan Pharmaceutical Machinery offers suppository machine in USA & Canada.
ReplyDeleteDryer service in dubai
ReplyDeletehttps://www.hometech.ae/service/dryer-service/
UAEs Authorized Major brand Dryer Service in Dubai, On-Demand experienced professionals for dryer service in Dubai.
1631943227638-7
kissanagroindustries.in are one of the prominent Dal Mill Plant Manufacturer in Delhi and supplier. These are developed from the best available technology and raw material. Our entire range of milling machines is known for their efficiency, accuracy, and excellent performance.
ReplyDeleteDal Mill Plant Is Used To Processing On Dal Like Masur, Lentils, Mataki, Tur, Urad, Chana, Etc. This Process Include Milling, Grinding, Grading, Polishing, Monitoring, Cleaning, Flour Making, And Removing Stones, Dust From Dal. To Get The Pure, Healthy, And Best Quality Dal, Buy Our Dal Mill Plant At A Market Leading Price.
You may also visit:
Dal Mill Plant Manufacturer in UP,
Seed Dryer Machine Manufacturer,
Batch Type Dryer Manufacturer,
Gravity Separator Machine manufacturer in Delh,
Dal Dryer Machine Manufacturer
Emkay Engineering is a Best Vacuum Planetary Mixer Manufacturer in India. we manufacture the optimum quality of Vacuum Planetary Mixer, which is used in various pharmaceutical applications. Excellent mixing efficiency and consistent performance, makes the planetary mixer highly demanded. We are provide Air Cooling Pad , Evaporative Cooling Pad, Cellulose Pad provide you the best quality at the best price.
ReplyDeleteChemical Reactor Manufacturers, Suppliers & Exporters in India
ReplyDeleteChemical Reactor Manufacturers,
ReplyDeleteLimpeted Reactor Manufacturers, Suppliers
ReplyDeleteJacketed Reactor Manufacturers, Suppliers
ReplyDeleteMixing Vessel Manufacturers, Suppliers
ReplyDeleteCondenser And Heat Exchanger Manufacturers, Suppliers
ReplyDeleteShell Heat Exchanger Manufacturers, Suppliers
ReplyDeleteSparkler Filter Manufacturers, Suppliers & Exporters
ReplyDeleteSigma Kneader Mixer Manufacturers, Suppliers
ReplyDeleteTube Heat Exchanger Manufacturers, Suppliers
ReplyDeleteFin Tube Heat Exchanger Manufacturers, Suppliers
ReplyDeleteIndustrial Dryers Manufacturers, Suppliers
ReplyDeleteAtmospheric Tray Dryer Manufacturers, Suppliers
ReplyDeleteVacuum Tray Dryer Manufacturers, Suppliers & Exporters
ReplyDeleteFluid Bed Dryer Manufacturers, Suppliers
ReplyDeleteSigma Mixer Manufacturers, Suppliers
ReplyDeleteSS Storage Tanks Manufacturers, Suppliers
ReplyDeleteSS Storage Tanks Manufacturers, Suppliers Rotary Cone Vacuum Dryer Manufacturers, Suppliers
ReplyDeleteRotary Vacuum Paddle Dryer (RVPD) Manufacturers, Suppliers
ReplyDeleteRibbon Roster Cum Dryer Manufacturers, Suppliers
ReplyDeleteBlenders Manufacturers, Suppliers & Exporters
ReplyDeleteRibbon Blender Manufacturers, Suppliers
ReplyDeleteDouble Cone Blender Manufacturers, Suppliers
ReplyDeleteHerbal Extraction Plant Manufacturers, Suppliers
ReplyDeletePharma Plant Manufacturers, Suppliers & Exporters
ReplyDeleteOctagonal Blender Manufacturers, Suppliers
ReplyDeleteCentrifuge Machines Manufacturers, Suppliers
ReplyDeleteNutsche Filter Manufacturers, Suppliers & Exporters
ReplyDeletePressure Nutsche Filter (PNF) Manufacturers, Suppliers
ReplyDeleteVacuum Nutsche Filter (VNE) Manufacturers, Suppliers & Exporters
ReplyDeletePharma Equipments Manufacturers, Suppliers
ReplyDeletePharmaceutical Equipment Manufacturers, Suppliers
ReplyDeleteYou did a very good submission and research about the topic.
ReplyDeletePharmaceutical Machinery - https://sspharmaequipment.com/
Great post! Concise and informative. Enjoyed reading it!
ReplyDeleteSultamicillin Tosilate 375 mg
Cefpodoxime Proxetil Tablets
Great post! Really enjoyed the insights.
ReplyDeleteBest Primary School in Panchkula, Haryana
Top Ranked School in Panchkula
Top 10 Nursery Schools in Panchkula
Top 10 Primary Schools in Panchkula
Best School in Panchkula
How to Choose the Best School for 1st Class Children in Panchkula